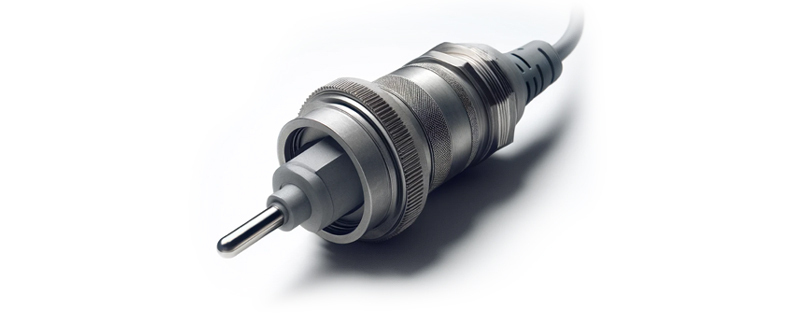
Beskyttelse af sensorer ved høje temperaturer
Sådan indstøber og beskytter du sensorer ved høje temperaturer med epoxy støbemasse
Ønsker du at beskytte elektroniske komponenter såsom sensorer selv ved høje temperaturer og på en måde der er nem at håndtere ?
Der findes limtyper, som epoxy specieldesignet til dette.
Ofte ser vi et behov for lime/støbemasser der er særdeles gode til at lime forskellige plasttyper såsom PA eller ABS.
Selv med PE kan man nå en kompressionsforskydningsstyrke på 20 MPa efter plasmaforbehandling, selvom denne billige og modstandsdygtige plast er svær at lime på grund af dens lave overfladespænding.
Vi anbefaler naturligvis at du kontakter os for den helt rigtige løsning til din applikation. Men med fast indstøbning (brudforlængelse 5%) og en temperaturbestandighed på op til 180 °C er vores indstøbningsepoxy ofte en perfekt valg.
Efter 1000 timers opbevaring ved maksimal brugstemperatur eller ved 85 °C og 85 % luftfugtighed forbliver produktets mekaniske egenskaber uændrede.
Derudover er limen modstandsdygtig over for olie og brændstof, som gør den særligt velegnet til anvendelse i motorrum – for eksempel til indstøbning af sensorer og printplader eller til tætning af konstruktioner.
Epoxyharpiksen opnår denne stabilitet uden nogen fyldstoffer og dette giver mange fordele med hensyn til forarbejdning.
Der er ikke risiko for at fyldstoffet bundfælder og derfor kræver denne type indstøbningsmasse hverken omrøring eller afgasning og det resulterer i et enklere systemdesign.
Epoxy støbemasserne er desuden designet med en god flydeevne, som ligeledes forenkler processen.
Disse epoxy indstøbningsmasser fås både som 1-komponent og 2-komponent.
Dispenserpistoler med statisk blanderør giver dog fornemmelsen af at arbejde med 1-komponent lim.
De kan både bruges til fuldautomatisk produktion og er også velegnet til halvautomatiske/manuelle processer.
Hærdetiden er udviklet til hurtige processen (eksempelvis udhærdning på 10 min), men kan alt efter epoxytype kræver opvarmning efter dosering.
Alternativt kan man arbejde med længere hærdetider og derved spare energi/omkostninger.
Kontakt os
Har du spørgsmål om limning eller behov for rådgivning om valg af den rette lim til din applikation? Vores eksperter står klar til at hjælpe dig med at opnå pålidelig og holdbar limning.
Vi tilbyder løsninger med limprodukter, der er skræddersyet til at imødekomme dine specifikke behov.
Kontakt os i dag for at få professionel rådgivning og support.
Ring til os på +45 66171802 for at tale direkte med en af vores specialister, eller send os en e-mail på info@hojstrup.dk.
Vi sikrer, at du får den bedste vejledning og support til dine limningsprojekter.